
Alloy surface treatment: a key process to improve product texture and durability
In modern manufacturing, the application range of alloy materials is expanding day by day. However, only relying on the basic metal material is often unable to meet the comprehensive requirements of high strength, corrosion resistance and aesthetics. At this time, "alloy surface treatment" has become an indispensable part. Through the professional processing of the alloy surface, the performance of the product can be greatly improved, while extending its service life.
Explore the importance of alloy surface treatment and its wide application in the industrial field
Whether it is aerospace parts or household appliance housings, almost all products involving precision manufacturing are inseparable from the support of alloy surface treatment. This process can not only strengthen the physical characteristics of the parts (such as wear resistance, heat resistance), but also increase the visual appeal through coloring or polishing. More importantly, a good surface protection layer can prevent damage to the substrate caused by the external environment, thereby ensuring long-term stable operation.
Reveal the characteristics of mainstream alloy surface treatment technology and analysis of applicable scenarios
At present, the common alloy surface treatment methods on the market include anodizing, electroless nickel plating, spraying and electrophoretic coating. Among them, anodic oxidation because of its excellent corrosion resistance and colorful appearance by the user's favorite; and chemical nickel plating is due to the advantages of uniform and dense coating is particularly suitable for complex geometry workpiece needs.
From oxidation to electroplating: in-depth analysis of the actual operation of various specific processes
Taking anodic oxidation as an example, this method usually requires the aluminum alloy to be immersed in a specific electrolyte solution, and the aluminum ions are deposited on the surface of the object to form a hard transparent film under the action of a direct current. Subsequent dyeing and sealing steps complete the process. Electroplating, in contrast, is the construction of a new outer structure by the attachment of metal particles to the object to be treated by means of an electric current.
Practical Case Sharing-The Story of Successfully Using Surface Treatment to Optimize Product Quality
a well-known kitchenware brand has faced the problem of stainless steel pot body rust for a long time. Later, they used advanced micro-arc oxidation technology to modify its inner wall, which not only solved the original defects but also enhanced the thermal conductivity efficiency. Customer feedback shows that the new product has a better cooking experience and cleaning maintenance is more convenient and efficient.
Discussion on the factors to be considered when selecting the appropriate surface treatment scheme
Choosing the right technology for different project contexts is critical. First of all, it is necessary to make clear the expected target effect, such as whether to pay attention to gloss or hardness index, and secondly, it is necessary to consider budget constraints, time arrangement and other factors to make a comprehensive judgment, so as to ensure that the final result is both economical and can fully show the ideal quality characteristics.
Future Trends: How Emerging Technologies Redefine the Alloy Surface Treatment Industry
With the success of nano-scale thin film development and the popularity of green environmental protection, more and more innovative solutions are emerging. For example, the use of water-soluble coatings to replace traditional oily substances to reduce pollution emissions and meet the requirements of international standards and regulations is expected in the near future these advances will further promote the development of the industry to a higher level.
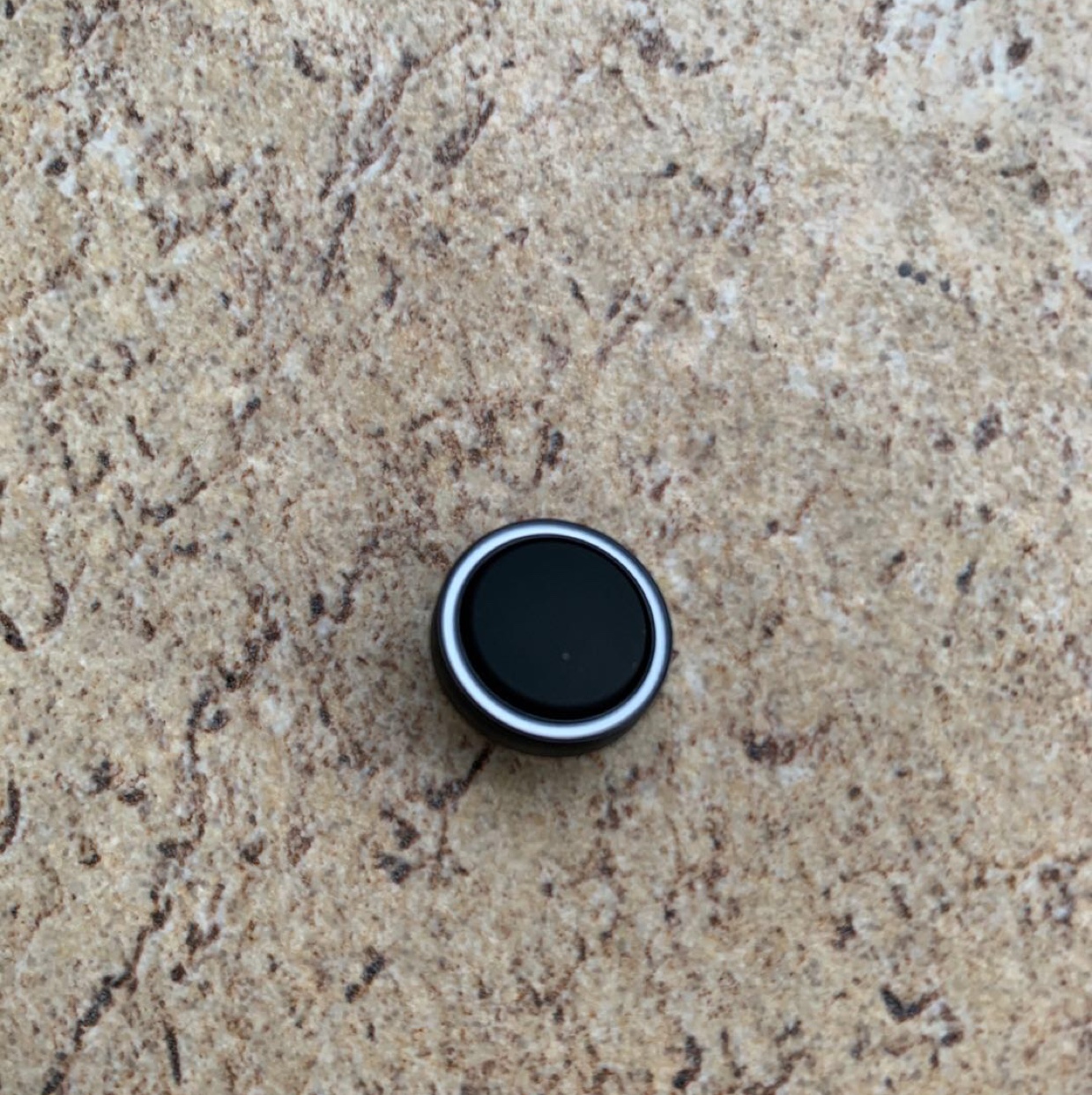